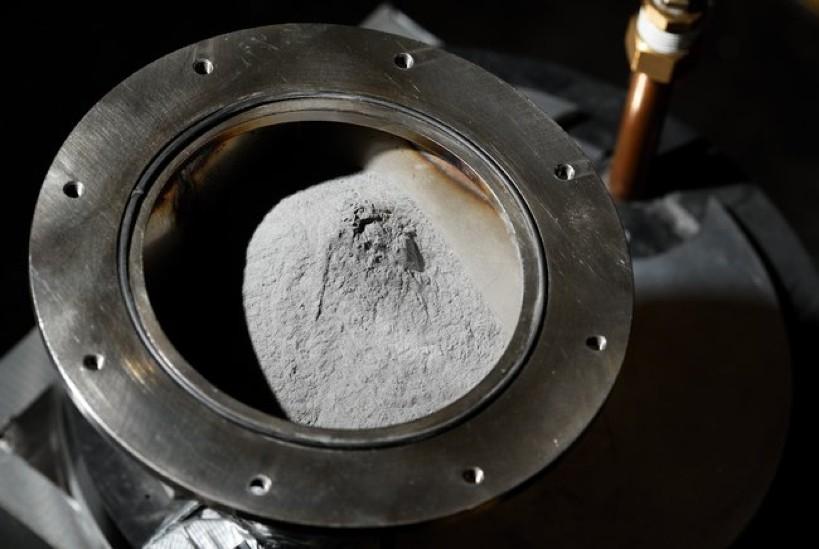
Futuro em pó
A empresa sueca VBN Components produz produtos siderúrgicos utilizando tecnologias aditivas utilizando pó com aditivos, principalmente ferramentas como brocas e fresas. A tecnologia de impressão 3D elimina a necessidade de forjamento e usinagem, reduz o consumo de matéria-prima e oferece aos usuários finais uma escolha mais ampla de materiais de alta qualidade.
A oferta de componentes VBN inclui, por exemplo. Vibenite 290que, segundo a empresa sueca, é o aço mais duro do mundo (72 BQ). O processo de criação do Vibenite 290 é aumentar gradualmente a dureza dos materiais até. Uma vez que as peças desejadas são impressas a partir desta matéria-prima, não é necessário nenhum outro processamento além de moagem ou EDM. Não é necessário cortar, fresar ou perfurar. Assim, a empresa cria peças com dimensões de até 200 x 200 x 380 mm, cuja geometria não pode ser produzida com outras tecnologias de fabricação.
O aço nem sempre é necessário. Uma equipe de pesquisa da HRL Laboratories desenvolveu uma solução de impressão 3D. ligas de alumínio com alta resistência. É chamado método nanofuncional. Simplificando, a nova técnica consiste em aplicar pós nanofuncionais especiais a uma impressora 3D, que são então “sinterizados” com camadas finas de laser, o que leva ao crescimento de um objeto tridimensional. Durante a fusão e solidificação, as estruturas resultantes não são destruídas e mantêm sua resistência total devido às nanopartículas que atuam como centros de nucleação para a microestrutura pretendida da liga.
Ligas de alta resistência, como o alumínio, são amplamente utilizadas na indústria pesada, tecnologia de aviação (por exemplo, fuselagem) e peças automotivas. A nova tecnologia de nanofuncionalização lhes confere não apenas alta resistência, mas também uma variedade de formas e tamanhos.
Adição em vez de subtração
Nos métodos tradicionais de usinagem, o material residual é removido por usinagem. O processo aditivo funciona ao contrário - consiste em aplicar e adicionar camadas sucessivas de uma pequena quantidade de material, criando peças XNUMXD de praticamente qualquer forma com base em um modelo digital.
Embora essa técnica já seja amplamente utilizada tanto para prototipagem quanto para fundição de modelos, seu uso direto na produção de bens ou dispositivos destinados ao mercado tem sido dificultado devido à baixa eficiência e propriedades insatisfatórias do material. No entanto, esta situação está mudando gradualmente graças ao trabalho de pesquisadores em muitos centros ao redor do mundo.
Através de experimentação meticulosa, as duas principais tecnologias de impressão XNUMXD foram aprimoradas: deposição de metal a laser (LMD) eu fusão seletiva a laser (ULM). A tecnologia laser permite criar detalhes finos com precisão e obter uma boa qualidade de superfície, o que não é possível com a impressão por feixe de elétrons 50D (EBM). No SLM, o ponto do feixe de laser é direcionado para o pó do material, soldando-o localmente de acordo com um determinado padrão com precisão de 250 a 3 mícrons. Por sua vez, o LMD usa um laser para processar o pó para criar estruturas XNUMXD autoportantes.
Esses métodos provaram ser muito promissores para a criação de peças de aeronaves. e, em particular, a deposição de metal a laser expande as possibilidades de design para componentes aeroespaciais. Eles podem ser feitos de materiais com estruturas internas complexas e gradientes que não eram possíveis no passado. Além disso, ambas as tecnologias de laser permitem criar produtos de geometria complexa e obter funcionalidade estendida de produtos de uma ampla gama de ligas.
Em setembro passado, a Airbus anunciou que havia equipado sua produção A350 XWB com impressão aditiva. suporte de titânio, fabricado pela Arconic. Este não é o fim, porque o contrato da Arconic com a Airbus prevê a impressão 3D a partir de pó de titânio-níquel. partes do corpo i sistema de propulsão. No entanto, deve-se notar que a Arconic não usa tecnologia a laser, mas sua própria versão aprimorada do arco eletrônico EBM.
Um dos marcos no desenvolvimento de tecnologias aditivas em metalurgia provavelmente será o primeiro protótipo apresentado na sede do Dutch Damen Shipyards Group no outono de 2017. hélice de navio liga de metal com o nome VAAMpeller. Após os devidos testes, a maioria já realizados, o modelo tem chance de ser aprovado para uso a bordo de navios.
Como o futuro da tecnologia metalúrgica está em pós de aço inoxidável ou componentes de liga, vale a pena conhecer os principais players desse mercado. De acordo com o "Relatório de mercado Additive Manufacturing Metal Powder" publicado em novembro de 2017, os fabricantes mais importantes de pós metálicos para impressão 3D são: GKN, Hitachi Chemical, Rio Tinto, ATI Powder Metals, Praxair, Arconic, Sandvik AB, Renishaw, Höganäs AB , Metaldyne Performance Group, BÖHLER Edelstahl, Carpenter Technology Corporation, Aubert & Duval.
Impressão de hélice WAAMpeller
Fase líquida
As tecnologias de aditivos metálicos mais conhecidas atualmente contam com o uso de pós (é assim que a vibração acima mencionada é criada) "sinterizados" e fundidos a laser nas altas temperaturas necessárias para o material de partida. No entanto, novos conceitos estão surgindo. Pesquisadores do Laboratório de Engenharia Criobiomédica da Academia Chinesa de Ciências em Pequim desenvolveram um método Impressão 3D com "tinta", constituído por uma liga metálica com ponto de fusão ligeiramente acima da temperatura ambiente. Em um estudo publicado na revista Science China Technological Sciences, os pesquisadores Liu Jing e Wang Lei demonstram uma técnica para impressão em fase líquida de ligas à base de gálio, bismuto ou índio com a adição de nanopartículas.
Em comparação com os métodos tradicionais de prototipagem de metal, a impressão 3D em fase líquida tem várias vantagens importantes. Primeiro, uma taxa relativamente alta de fabricação de estruturas tridimensionais pode ser alcançada. Além disso, aqui você pode ajustar com mais flexibilidade a temperatura e o fluxo do líquido de arrefecimento. Além disso, o metal condutor líquido pode ser usado em combinação com materiais não metálicos (como plásticos), o que expande as possibilidades de design para componentes complexos.
Cientistas da American Northwestern University também desenvolveram uma nova técnica de impressão 3D de metal que é mais barata e menos complexa do que a conhecida anteriormente. Em vez de pó de metal, lasers ou feixes de elétrons, ele usa forno convencional i material líquido. Além disso, o método funciona bem para uma ampla variedade de metais, ligas, compostos e óxidos. Isso é semelhante à vedação do bico que conhecemos com plásticos. A "tinta" consiste em um pó metálico dissolvido em uma substância especial com a adição de um elastômero. No momento da aplicação, está em temperatura ambiente. Depois disso, a camada de material aplicada do bico é sinterizada com as camadas anteriores a uma temperatura elevada criada no forno. A técnica é descrita na revista especializada Advanced Functional Materials.
Método chinês de impressão em fase de metal líquido
Em 2016, pesquisadores de Harvard introduziram outro método que pode criar estruturas metálicas XNUMXD. impresso "no ar". A Universidade de Harvard criou uma impressora 3D que, ao contrário de outras, não cria objetos camada por camada, mas cria estruturas complexas "no ar" - a partir de metal congelado instantaneamente. O dispositivo, desenvolvido na Escola de Engenharia e Ciências Aplicadas John A. Paulson, imprime objetos usando nanopartículas de prata. O laser focado aquece o material e o funde, criando várias estruturas, como uma hélice.
A demanda do mercado por produtos de consumo impressos em 3D de alta precisão, como implantes médicos e peças de motores de aeronaves, está crescendo rapidamente. E como os dados do produto podem ser compartilhados com outras empresas, empresas em todo o mundo, se tiverem acesso a pó de metal e à impressora 3D certa, podem trabalhar para reduzir os custos de logística e estoque. Como se sabe, as tecnologias descritas facilitam muito a fabricação de peças metálicas de geometria complexa, à frente das tecnologias tradicionais de produção. O desenvolvimento de aplicações especializadas provavelmente levará a preços mais baixos e abertura ao uso da impressão 3D em aplicações convencionais também.
O aço sueco mais duro - para impressão 3D:
O aço mais duro do mundo - fabricado em Uppsala, Suécia
Filme de alumínio para impressão:
Avanço na metalurgia: impressão 3D de alumínio de alta resistência

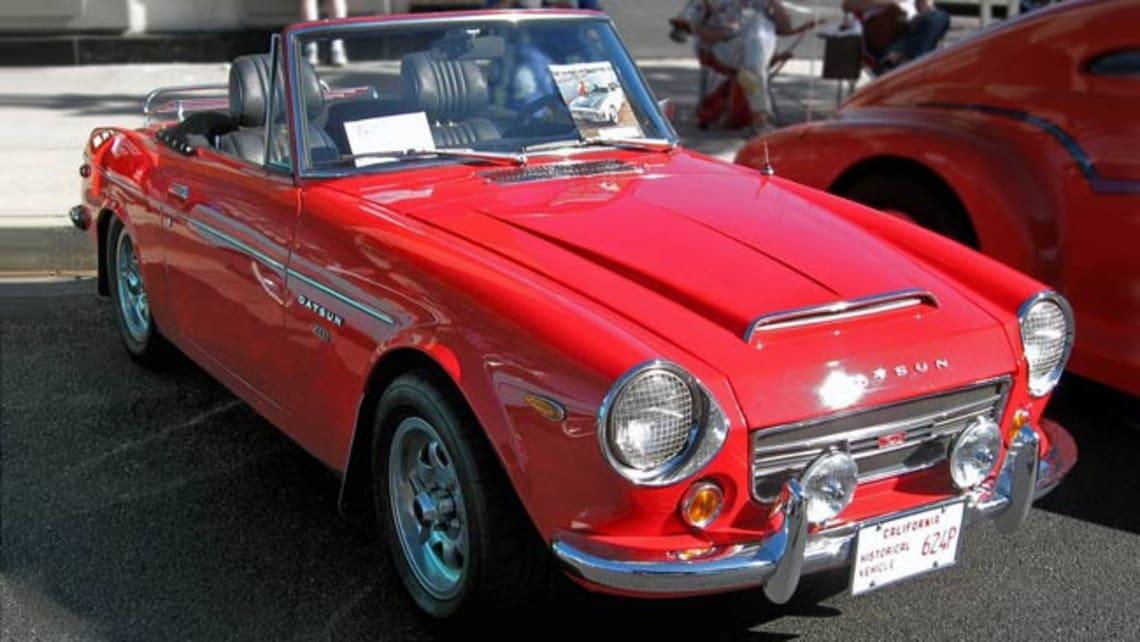
Um comentário
Anônimo
Piada